Polishing methods for clear mirror aluminum sheet
There are three polishing methods for clear mirror aluminum sheet: mechanical polishing, electrolytic polishing and chemical polishing. Mechanical polishing is generally the operation of pressing an aluminium sheet onto a rotating cloth wheel or other elastic wheel pre-coated with a polishing paste. The essence is to use the polishing wheel to smooth the extremely small unevenness on the surface. The aluminum sheet can be mechanically polished to obtain a mirror-like surface, and its color varies with the polishing paste used. Electrolytic polishing is to use an aluminum sheet as the anode. During the electrolysis process, the protruding speed of the protruding part of the sheet is higher than that of the low recess. As the polishing progresses, the microscopic and macroscopic convex and concave portions of the sheet surface are completely This process improves the micro-geometry of the metal surface, reduces the micro-roughness of the metal surface, and the aluminum profile brightens the surface of the part.
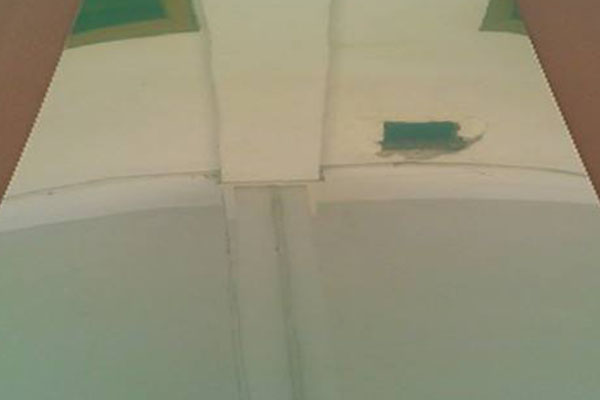
Electrolytic polishing for the clear mirror aluminum sheet can be used to replace heavy mechanical polishing, especially in the shape of complex, mechanically difficult to machines. However, electrolytic polishing cannot remove non-gold inclusions in the gold period, nor can it remove or mask surface defects such as scratches and deep pitting on the sheet surface. In a multiphase alloy, when one phase is not easily dissolved in the anode, which will affect the quality. Chemical polishing is the chemical etching of metal parts under certain conditions. During this etching process, the metal surface is etched and leveled by the solution to obtain a relatively bright surface.
Chemical polishing can be used in the manufacturing clear mirror aluminum sheet for instruments and the decorative processing of other parts and coatings. Compared with electrolytic polishing, chemical polishing has a higher production efficiency, but the surface quality is generally slightly lower. It is also difficult to adjust and regenerate the solution. In the polishing process, harmful gases such as nitrogen oxides are precipitated. In the process of electrolytic polishing, the surface of the anode is formed. During the chemical polishing process, either due to the formation of a non-uniform passivation film on the microscopic surface of the metal, or due to the formation of a thick sticky similar to that occurring during electro-polishing so that the surface micro-convex portions dissolution rate significantly greater than the micro-concave portion, thus reducing the microscopic roughness of the surface of the aluminum sheet, the part of the surface of relatively light and smooth.
评论
发表评论