Black anodized aluminum sheets
Black anodized aluminum sheets are obtained by anodizing and coloring the surface of targeted aluminium sheets. Anodizing is a material protection technology for an aluminum plate to form oxide film on its surface by applying anode current in electrolyte solution. Cast aluminum can be black by common anodizing. After anodizing, the sheet is dyed with a black solution: acid MaoYuan att 20-30g / L acid lake blue 2-3g / L temperature 50-70 ℃ time 10-15min pH 3-3.5 (or 4.5-5.5). Film thickness can be made according to the requirements of customers, generally 10 to 20 microns. In comparison to original color anodizing, black anodizing takes an extra process and a longer time, thus it costs more.
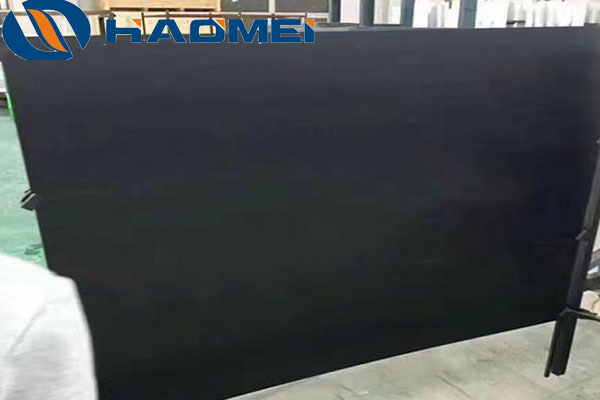
A black anodized aluminum sheet is widely used in mechanical parts, aircraft and automobile parts, precision instruments and radio equipment, building decoration, lighting, electronic products, handicrafts, home appliances, interior decoration, signs, furniture, automobile decoration and so on. In interior and exterior decoration it is made into metal aluminum ceiling, curtain wall panels, aluminum plastic panels, fireproof panels, bee side aluminum panels, aluminum veneers, cabinet panels, furniture panels, etc.
The outer layer of anodizing film of aluminum is porous and easy to absorb dyes and colored substances, so it can be dyed to improve its decoration. After being sealed by hot water, high temperature steam or nickel salt, the corrosion resistance and wear resistance of the oxide film can be further improved. Theoretically many alloys of aluminium can be made into black anodized aluminium sheets, but 5000 series, including 5005, 5754, 5182, 5052 and 5083, prove to be the best materials for anodizing. Anodized 5xxx sheets display ideal hardness, corrosion resistance and service life, winning increasing popularity in the electronic industry.
评论
发表评论